Top 5 Mistakes to Avoid When Using UPC and EAN Barcodes in Your Business
In the world of business today, using barcodes like UPC and EAN is crucial for keeping things organized and running smoothly. These barcodes help manage your inventory, speed up transactions, and make operations more efficient. However, businesses often face challenges because of common mistakes when using these barcodes.
This article is here to help you by pointing out the top 5 mistakes businesses often make with UPC and EAN barcodes. By understanding and avoiding these mistakes, you can use barcodes effectively, ensuring accuracy, efficiency, and happy customers. We’ll explore the details of barcode usage to show that paying attention to these details is essential for making the most of UPC and EAN barcodes in your business.
I. Choosing the Wrong Barcode Type
- UPC and EAN serve as identification codes for products.
- UPC is widely used in North America, while EAN is more common internationally.
- Knowing the difference helps businesses choose the right barcode for their market.
B. Matching Barcodes to Product Needs
- Each product may have specific requirements for barcode usage.
- Consideration should be given to factors like product type, target market, and distribution channels.
- Choosing the wrong barcode may lead to complications in tracking and sales.
C. Importance of Accurate Barcode Selection
- Selecting the right barcode type is crucial for efficient product tracking.
- The correct barcode choice ensures compatibility with industry standards and market expectations.
- By paying attention to product needs and market specifications, businesses can avoid the pitfalls of using the wrong barcode type.
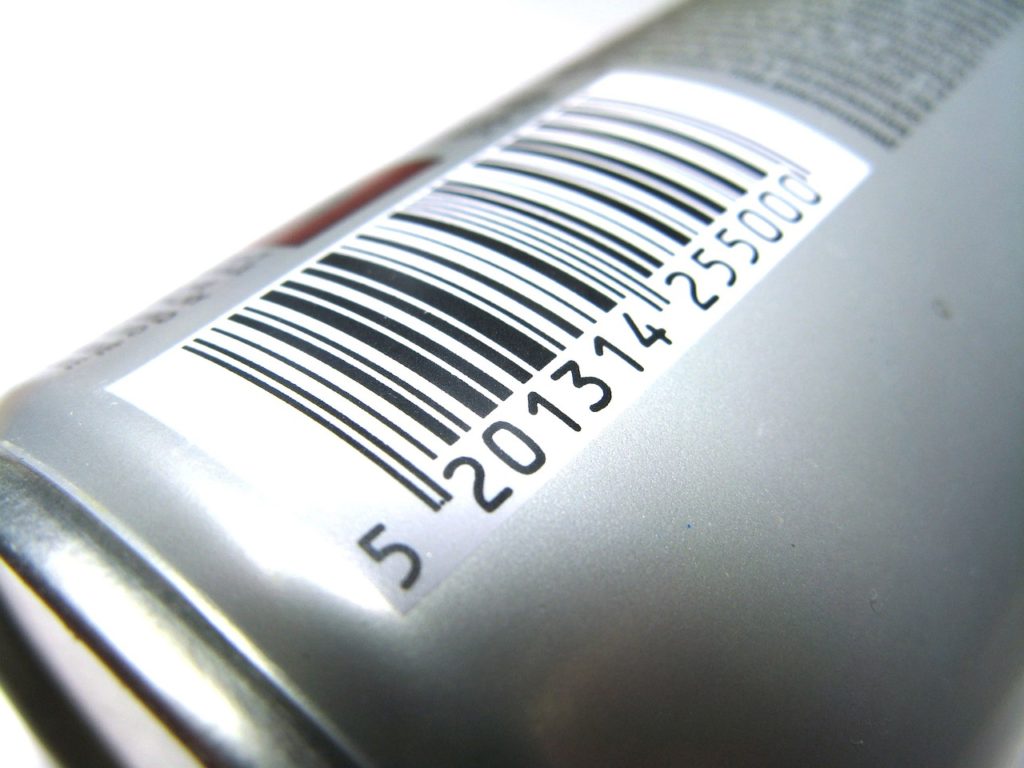
II. Incorrect Barcode Placement
A. Significance of Proper Barcode Placement
- Proper placement of barcodes is essential for effective scanning.
- Barcode scanners rely on clear visibility to quickly and accurately read information.
- Well-placed barcodes contribute to smooth inventory management and checkout processes.
B. Avoiding Common Errors in Placement
- Barcodes should be placed on flat surfaces without folds, wrinkles, or interference.
- Avoid placing barcodes on corners, edges, or uneven surfaces, which can hinder scanning.
- Ensuring consistent and standardized barcode placement across products is vital.
C. Impact of Incorrect Placement on Efficiency
- Incorrectly placed barcodes can result in scanning errors and delays.
- Inaccuracies in tracking and checkout processes may lead to customer dissatisfaction.
- Businesses should prioritize clear guidelines for barcode placement to maintain efficiency and accuracy in their operations.
III. Inadequate Barcode Printing Quality
A. The Importance of High-Quality Barcode Printing
- Clear and well-printed barcodes are crucial for reliable scanning.
- High-quality printing ensures that scanners can read barcodes accurately, minimizing errors.
- Faded, smudged, or distorted barcodes can lead to scanning failures and operational disruptions.
B. Common Issues Related to Low-Quality Printing
- Low-resolution printing may result in unclear barcodes that are challenging to scan.
- Inconsistent printing materials and techniques can compromise barcode visibility.
- Barcodes printed on substandard surfaces may wear off over time, affecting durability.
C. Investing in Suitable Printing Technology and Materials
- Businesses should invest in quality printing technology to produce clear and readable barcodes.
- Selecting appropriate printing materials, such as label stock and ink, ensures longevity.
- Regularly checking and maintaining printing equipment helps prevent issues and guarantees barcode quality.
IV. Failing to Integrate Barcodes with Inventory Management Systems
A. Importance of Integrating Barcodes with Inventory Management
- Barcodes are integral to effective inventory management systems.
- Seamless integration facilitates real-time tracking, reduces errors, and enhances efficiency.
- Neglecting integration may lead to discrepancies in inventory records and hinder overall business operations.
B. Consequences of a Lack of Integration
- Manual data entry without barcode integration increases the risk of human errors.
- Inefficient inventory tracking may result in stockouts, overstock situations, and loss of revenue.
- Inability to access real-time data can impede decision-making and strategic planning.
C. Implementing Seamless Barcode and Inventory Management System Integration
- Businesses should invest in software solutions that integrate barcode data with their inventory management systems.
- Regularly updating and synchronizing barcode data with inventory databases ensures accuracy.
- Training staff on the integrated system promotes smooth operations and maximizes the benefits of barcode technology in inventory management.
V. Failure to Regularly Update Product Information
A. The Significance of Keeping Product Information Up-to-Date
- Timely updates of product information are crucial for accurate barcode functionality.
- Changes in pricing, packaging, or product details require immediate updates to avoid discrepancies.
- Outdated information can lead to confusion, errors in tracking, and potential customer dissatisfaction.
B. Risks of Using Outdated Barcode Data
- Pricing errors can occur if barcode information does not reflect current product prices.
- Changes in packaging, such as size or design, may not be accurately represented in outdated barcodes.
- Consumer trust can be eroded if discrepancies between barcode information and actual products are detected.
C. Implementing a System for Regular Updates and Maintenance
- Establishing a process for regular updates ensures that barcode information aligns with the latest product data.
- Utilizing inventory management systems with automated update features reduces the likelihood of manual errors.
- Regular audits and reviews of barcode data help identify and rectify discrepancies promptly, maintaining accuracy in product information.
In Closing: Mistakes To Avoid When Using EAN And UPC Barcodes
In wrapping up, using UPC and EAN barcodes in business is a big deal. We’ve covered the common mistakes to avoid, and it’s clear that paying attention to the little things matters a lot. Whether it’s picking the right barcode, placing it correctly, or keeping things up-to-date, each step plays a key role.
Steering clear of slip-ups like putting barcodes in the wrong place or using low-quality printing is vital. These mistakes can lead to scanning errors and mess up inventory records, impacting customer satisfaction and business success.
To end on a good note, keep training your staff, stick to industry rules, and always aim to get better. Businesses that handle UPC and EAN barcodes well not only make their processes smoother but also make customers happier.
In a nutshell, businesses that handle UPC and EAN barcodes smartly set themselves up for success in today’s competitive business world.